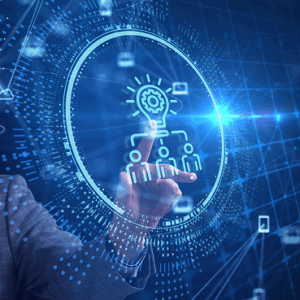
OptimaX
OptimaX is a real-time AI-powered tool for optimizing equipment performance in oil & gas and chemical industries. It monitors production, energy, and sustainability KPIs to identify operational inefficiencies. Live data analytics and color-coded insights highlight gaps from ideal conditions. Engineers receive actionable guidance on how to adjust process parameters, improving yields and reducing energy use. With advanced dashboards, heat maps, and sensitivity analysis, OptimaX transforms reactive monitoring into predictive, data-driven performance enhancement—driving digital transformation across refineries and process industries.
Salient Features
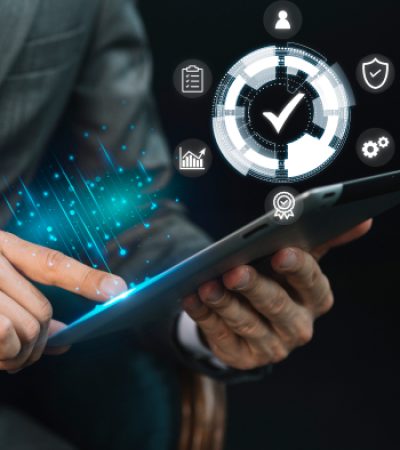
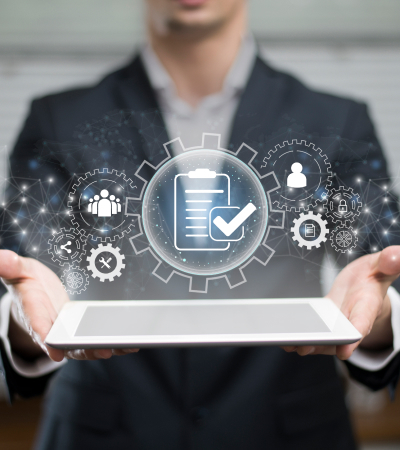
Client Benefits
3–7% Higher Asset Throughput
Maximize equipment utilization through real-time performance insights and optimization KPIs.
30% Faster Operational Decisions
Enable faster corrective actions using live gap analysis and predictive visualizations.
5–10% Improved Plant Efficiency
Optimize operations dynamically by adjusting to real-time plant conditions and KPI fluctuations.
40% Reduction in Manual Monitoring
Automate performance tracking, bottleneck detection, and reporting across units.
25% Faster Root Cause Analysis
Accelerate troubleshooting with integrated diagnostics and historical pattern recognition.
Dashboard & Snapshots
Case Studies
Development of Soft Sensor to predict the C5 contents in Debutaniser column Overhead:
Background
In modern petrochemical operations, maintaining product specifications within tight limits is critical for both quality assurance and process efficiency. One of the key challenges faced by a leading chemical plant was the need for real-time prediction and monitoring of C5 content in the overhead stream of the debutanizer column — a crucial step to ensure product specification compliance and optimize operations.
Challenge
Traditional laboratory testing methods for measuring C5 content introduced significant time delays, making real-time adjustments difficult. The plant required a fast, accurate, and reliable solution to continuously monitor C5 levels, allowing operators to take timely corrective actions and avoid off-spec products.
Solution with AnalyticX
Using AnalyticX, the engineering team was able to develop a soft sensor — a machine learning-based predictive model — specifically designed to estimate the C5 content in the debutanizer overhead stream in real time.
Key steps included:
- Seamless ingestion of historical operational data into AnalyticX without any coding requirements.
- Applying statistical analysis to identify key process variables influencing C5 concentrations.
- Rapid development and training of a machine learning model tailored to predict C5 content with high accuracy.
- Deployment of the predictive model into live operations for real-time product spec monitoring.
Results
- Enhanced Product Monitoring:
Operators now have a real-time view of the predicted C5 content, significantly reducing reliance on delayed lab measurements. - Improved Process Control:
By closely tracking C5 levels, the plant was able to make timely adjustments to operational parameters, ensuring consistent product quality. - Reduced Off-Spec Production:
Real-time insights helped minimize off-spec batches, leading to material savings and reduced reprocessing costs.
Key Takeaways
- AnalyticX enabled the rapid development of a soft sensor customized for critical KPI monitoring.