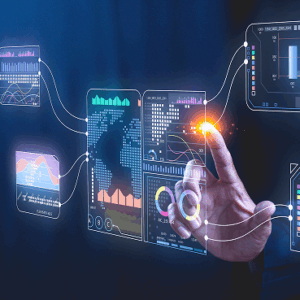
AnalyticX
Transform your plant operations with AnalyticX, the no-code analytics platform engineered for process industries. AnalyticX enables engineers to deploy predictive models, monitor KPIs in real time, and detect early anomalies—all without coding. Trusted in oil & gas and chemical manufacturing, it reduces downtime, enhances product quality, and speeds up decision-making. AnalyticX turns historical plant data into actionable insights using built-in AI and machine learning engines. Designed for field engineers, it closes the gap between operations and data science, driving efficiency and digital innovation across critical plant processes.
Salient Features
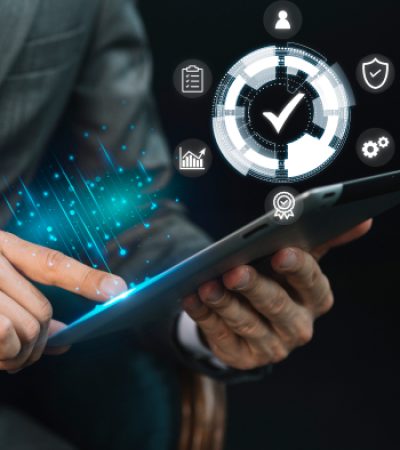
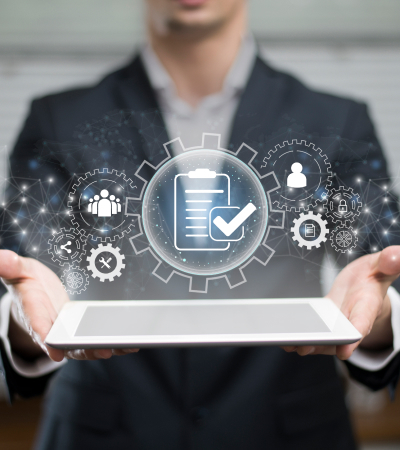
Client Benefits
30% Faster Insights
Accelerate decision-making with no-code predictive models and real-time dashboards.
25% Higher Production Yields
Optimize processes using AI-driven recommendations for critical parameters.
40% Lower Lab Costs
Replace manual testing with soft sensors for continuous quality monitoring.
50% Fewer Unplanned Shutdowns
Predict equipment failures weeks in advance with anomaly detection.
$1M+/Year Cost Savings
Minimize off-spec production and reduce energy waste through AI optimization.
Dashboard & Snapshots
Case Studies
Development of Soft Sensor to predict the C5 contents in Debutaniser column Overhead:
Background
In modern petrochemical operations, maintaining product specifications within tight limits is critical for both quality assurance and process efficiency. One of the key challenges faced by a leading chemical plant was the need for real-time prediction and monitoring of C5 content in the overhead stream of the debutanizer column — a crucial step to ensure product specification compliance and optimize operations.
Challenge
Traditional laboratory testing methods for measuring C5 content introduced significant time delays, making real-time adjustments difficult. The plant required a fast, accurate, and reliable solution to continuously monitor C5 levels, allowing operators to take timely corrective actions and avoid off-spec products.
Solution with AnalyticX
Using AnalyticX, the engineering team was able to develop a soft sensor — a machine learning-based predictive model — specifically designed to estimate the C5 content in the debutanizer overhead stream in real time.
Key steps included:
- Seamless ingestion of historical operational data into AnalyticX without any coding requirements.
- Applying statistical analysis to identify key process variables influencing C5 concentrations.
- Rapid development and training of a machine learning model tailored to predict C5 content with high accuracy.
- Deployment of the predictive model into live operations for real-time product spec monitoring.
Results
- Enhanced Product Monitoring:
Operators now have a real-time view of the predicted C5 content, significantly reducing reliance on delayed lab measurements. - Improved Process Control:
By closely tracking C5 levels, the plant was able to make timely adjustments to operational parameters, ensuring consistent product quality. - Reduced Off-Spec Production:
Real-time insights helped minimize off-spec batches, leading to material savings and reduced reprocessing costs.
Key Takeaways
- AnalyticX enabled the rapid development of a soft sensor customized for critical KPI monitoring.